Wireless Crack
Detection System
Structural health monitoring system to provide data-driven maintenance decisions.
When dealing with heavy-duty steel assets such as those found in industrial cranes and supporting structures, the integrity of every weld and joint is critical. However, the current method of monitoring steel structures, if at all done, involves substantial investment in resource, access equipment, time, and is very labour intensive.
Traditional NDT and inspection methods would typically mandate a specialist to visit the site, adding financial burden and risking operational disruptions. This outdated approach not only impacts your budget but also exposes assets to costly downtime.
Isn’t it time for a revolution in structural monitoring?
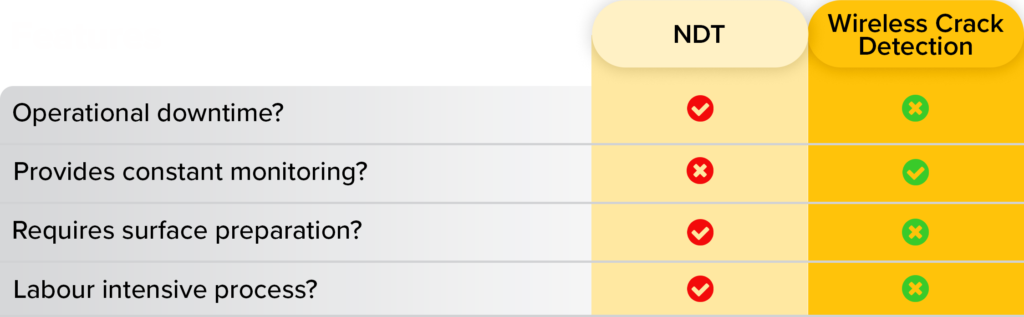
A Revolutionary Solution
Introducing the continuous wireless crack detection system offering unrivalled condition monitoring for key structural points in your steel structures.
- Sensor units provide local monitoring of critical joints or high-stress locations.
- Detects crack growth earlier than some of the best available Non-Destructive Testing solutions.
- Data is continuously updated in an easy-to-access online dashboard environment.
The innovative sensor technology is attached to the key structural points (welds, joints, etc.) of your steel structures, detecting small fractures or “fatigue cracks” via magnetic field fluctuations over time. Whilst NDT provides one sample at the time of the test, this detection system produces 6-8 samples a day. It compares data to crack progression with confidence, enabling easy monitoring via wireless transmission. Material integrity assessments are securely stored and tracked, promptly notifying of any necessary interventions.
Distributed and Installed by Street Cranexpress
The solution is new to the UK but already installed with several users, safeguarding assets including bridges owned by the Dutch Government and several industrial cranes at harbours and steel manufacturing sites in Europe.
High Accuracy
Competitive with state-of-the-art NDT methods.
No Surface Preparation
Apply our sensors directly on painted steel (no paint removal necessary).
Wireless
Data is transmitted wirelessly with SIM card connection, with low data volume.
Always Up to Date
Continuously updated online dashboard with automated warning emails.
Long Battery Life
Up to 5-years battery life for each sensor unit.
Plug and Play
Highly flexible design allows application in many different configurations
Attractive Pricing
Smart tech for affordable monitoring.
Certified
Holds a CE and UKCA Certification.
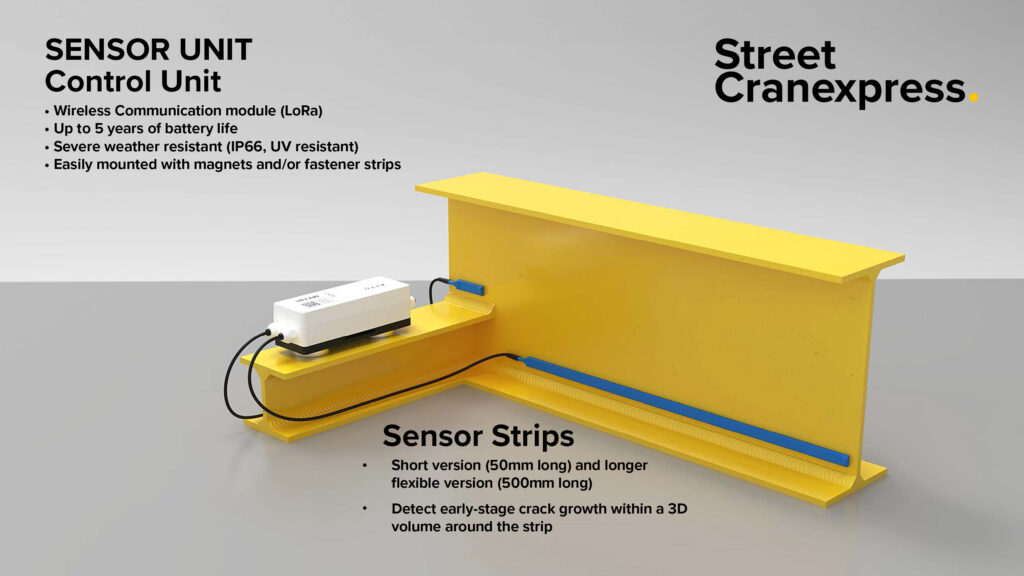
Sensing Capabilities of the
Sensor Strips
The sensors enable ongoing constant monitoring of steel structures, enabling the duty-holder to see in real-time as problems develop and when they need to take action, as in the example below.
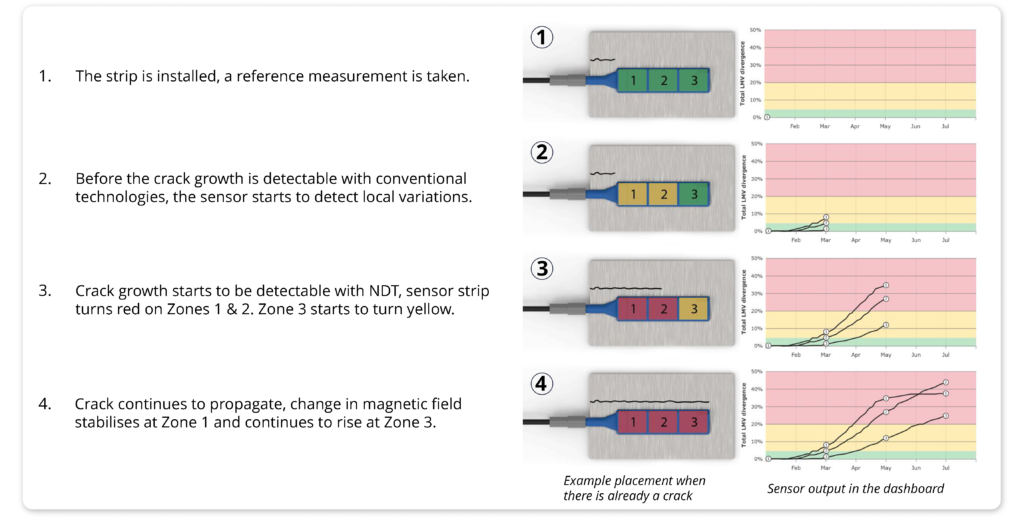
Automated Analysis in an Online Dashboard
Monitor the structural lifespan of aging assets securely and seamlessly, with a personalised online platform displaying asset summaries, sensor unit locations, and real-time fatigue crack updates in a user-friendly format. Users receive email or phone alerts if predefined thresholds are exceeded.
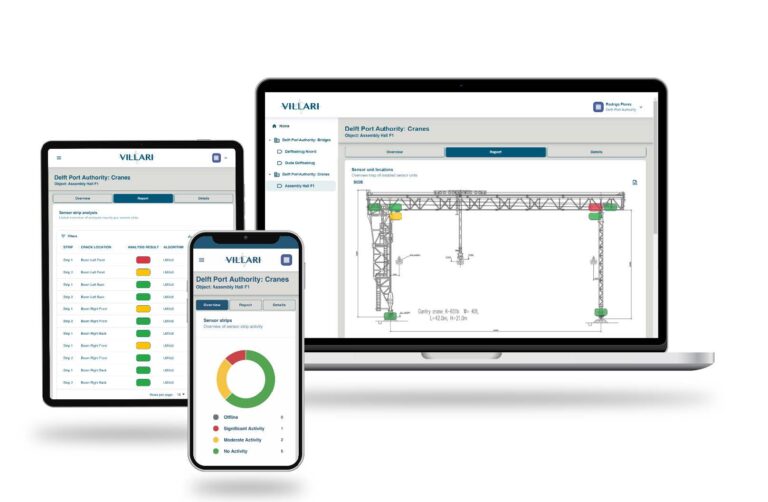
Industry Applications
The sensors cater to all owners of heavily burdened steel structures, as well as maintenance personnel overseeing bridges or cranes. They aim to monitor these assets safely and responsibly, while minimising the need for unscheduled maintenance.
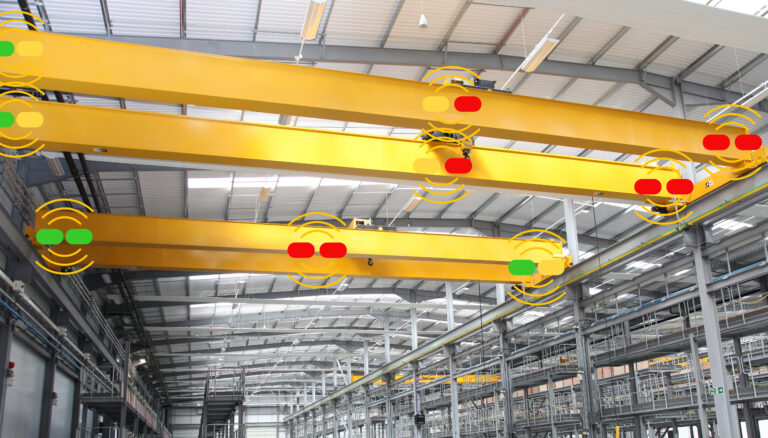
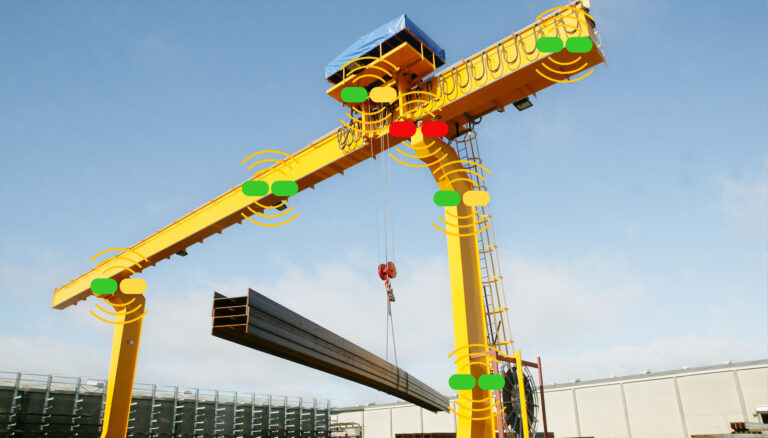
Due to the wide range of industrial applications, and the flexibility of its use, the wireless crack detection system caters for industries as varied as:
- Dockside cranes
- Steel building structures
- Overhead travelling cranes
- Construction
- Shipbuilding
- Facilities Management
- Bridges
- Industrial cranes
- Automotive engineering
- Manufacturing
- Steel workshops
Use Case - Reactive Placement
Continuously measure crack propagation in order to schedule inspection and repairs.
- Detectable crack growth can be both root and toe initiating (sub-surface) cracks
- Extensive documentation available upon request including both laboratory and field results
- Proven algorithm for crack detection, CE certified.
- Specification sheet available upon request.
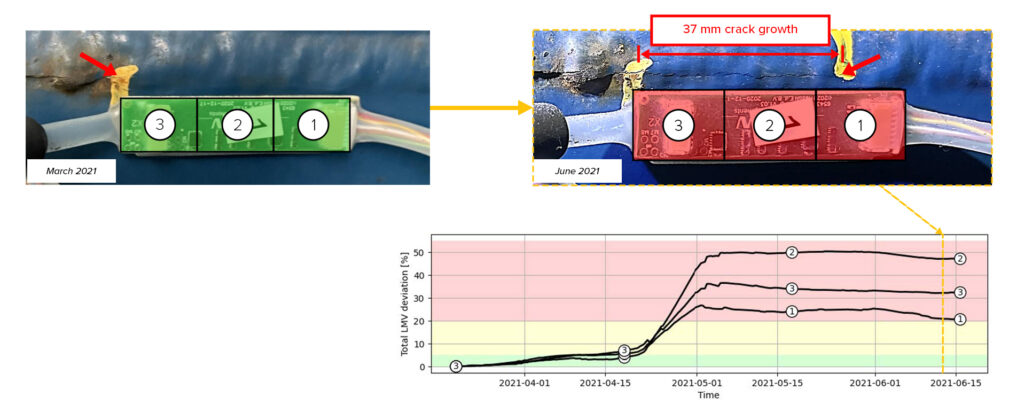
Use Case - Preventive Placement
Placing sensors on EOT crane as it reaches end-of-life to monitor asset and provide alerts to necessary interventions.
- Installation without a detected crack in Aug ’21
- During inspection in July ’22 a 21 mm crack was found using penetrant dye inspection, the system at this point already measured significant changes
- Moderate activity was detected by the sensors in October ’21, nine months before NDT discovered a crack
- Afterwards: no crack growth was visually reported but after reviewing the sensors’ data an additional 7 mm crack growth was found
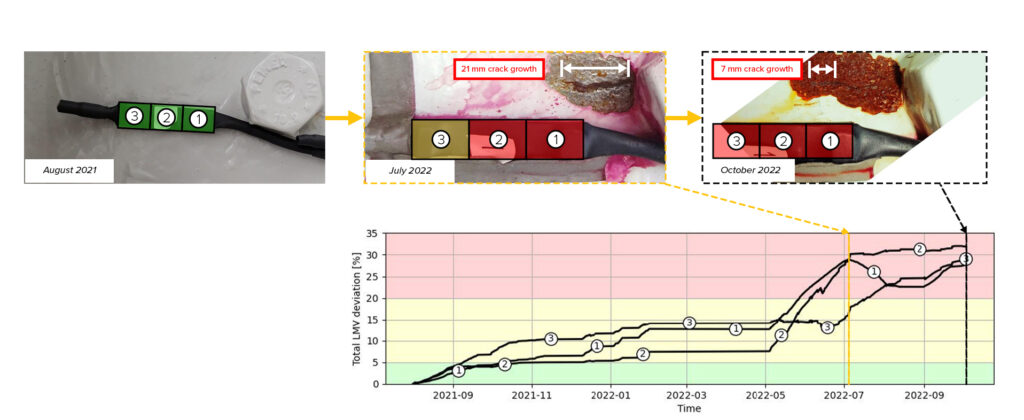
Continuous Monitoring
- Continuous information of crack growth, safer than inspecting every couple of months.
- Single installation moment, five years of monitoring
- Affordable with limited operational impact
- If crack growth is detected, the sensor is much earlier than a visual inspection and a crack repair can be scheduled months in advance.
- Comparable with having an NDT inspector checking the critical elements every day.
Villari Wireless Crack Detection System
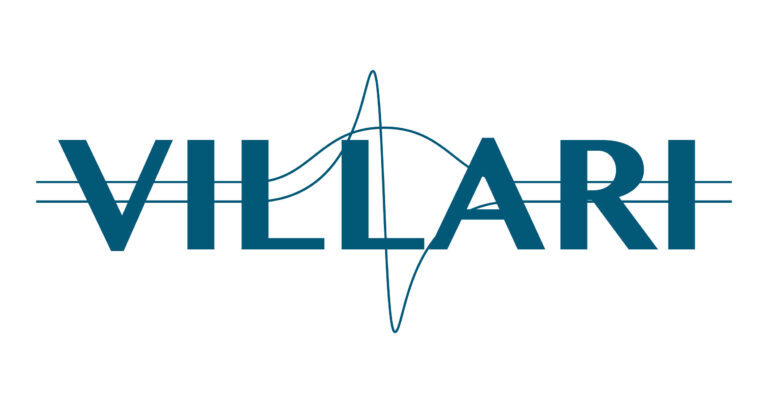
Street Cranexpress have partnered with Villari to distribute their innovative detection system exclusively within the UK. Villari is a start-up company based in the Netherlands with a passionate, dynamic team that are growing rapidly. Street Cranexpress are delighted to have partnered with Villari, and are excited to pioneer this product within our industry.
Get Started today
Enquire with us today to receive costs to implement the detection system on your steel structures.